Basic Introduction to Broiler Housing Environmental Control
By Brian D. Fairchild, Department of Poultry Science, University of Georgia - Broilers have been selected for increased meat yield, better feed conversion and high growth rates for many decades. Fifty years ago it took over 12 weeks to raise a 4 pound broiler. Through advances in genetic selection and nutrition, a 5 pound broiler can now be raised in 6 to 7 weeks.Introduction
Genetics and nutritional improvements in
broiler production have been extremely important to
the efficiency of poultry meat production; however, the
full genetic potential of broilers can not be reached unless
the proper environment is maintained in the broiler
house. The fast growing, modern broiler lines are more
dependent on proper environmental conditions than
birds from lines raised just a few years ago.
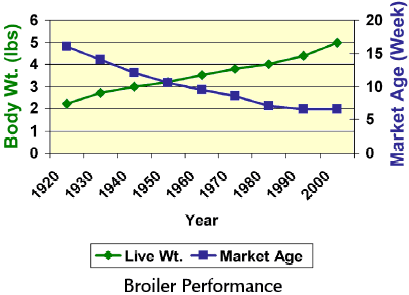
Construction
Broiler houses in the United States are constructed
with wood or steel trusses and supports. The houses are
clear span structures from side wall to side wall. The
trusses are engineered to support the weight of the roof
without the need of support posts that make it harder to
catch birds and clean out the house. The floor is typically
compacted dirt that is covered with bedding material (wood shavings, peanut hulls, rice hulls, sand,
etc.). House dimensions are usually 40-50 ft wide, 400-
600 ft long with 8 ft high sidewalls.
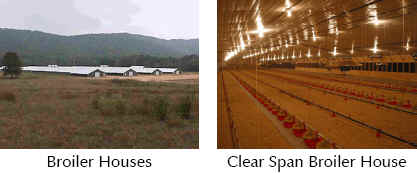
Dropped Ceilings:
To improve ventilation and reduce heating costs, most houses now have dropped ceilings. Dropped ceilings protect the trusses and ceiling insulation by acting as a vapor barrier. Dropped ceilings reduce the ceiling surface area and allows for the installation of ceiling insulation to reduce heat gain in during hot weather and heat loss during cold weather. Modern houses are well insulated with blown in cellulose or fiber glass batt insulation to reduce heat gain in the summer and heat loss in the winter. Insulation values of at least R-21 and R-7 are recommended in the ceiling and walls, respectively.
Solid Side Walls:
Most houses are constructed with solid side walls
rather than having open sides with curtains. This provides
better insulation, reduces air leaks, provides
better light control and allows the house to be heated
more efficiently. The use of solid side walls provides a
smooth surface compared to open sides walls with
posts. This improves air speed during tunnel ventilation
that will increase the cooling of birds next to the wall.
Another trend in new construction is the building of
larger houses. Houses as large as 70 x 600 ft have been
constructed. If these houses prove to be cost effective,
it is likely that most new houses will be constructed to
larger dimensions in the future.
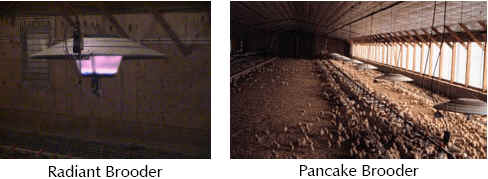
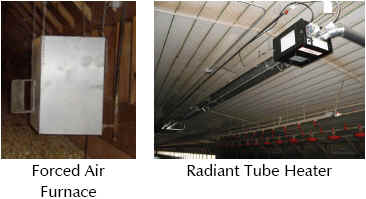
Heating
Maintaining proper temperature to promote efficient
growth is key to profitable broiler production. Thus,
heating a broiler house is extremely important from
both a performance and economic standpoint. Chicks
are not able to completely maintain their body temperature
until approximately 14 days of age. During this
time, it is crucial that floor temperature be maintained
between 85-90 degrees F with minimum variation. The
primary fuels used in heating U.S. broiler houses are
propane or natural gas. Broiler heating systems include
radiant brooders, pancake brooders, forced air furnaces
and radiant tube heaters. Brooders and tube heaters
project heat onto the floor. The hot air furnaces heat the
air, which then heats the floor.
Hot air is lighter than cold air. This can result in
stratification with the air being warmer at the ceiling
than at the floor. Circulation fans are often used to
move hot air from the ceiling down to the floor. Using
circulation fans to mix the warm and cool air can result
in as much as 30 percent fuel
savings and may improve
litter conditions as the warmer
air on the floor helps dry
litter. Paddle fans can also be
used to mix air, but be careful
to ensure that the chicks are
not exposed to drafts.
Ventilation
Ventilation delivers fresh air and removes excess heat, moisture and undesirable gases from the broiler house. A typical ventilation system in a broiler house consists of fans, air inlets, evaporative cooling system and controller/thermostats. Houses are designed to deal with both cold and hot weather extremes.
Cold Weather Ventilation:
During cold weather, negative pressure ventilation
is used to provide fresh air, remove moisture and minimize
heat loss. Fans exhaust air out of the house creating
a slight negative pressure inside the house. Fresh air
is pulled into the house due to the negative pressure and
enters through planned air inlets that are installed either
high on the house side wall or in the ceiling. These
inlets are designed to direct air across the ceiling
allowing it to mix with warmer air located there and to
heat up before coming into contact with the birds.
Newer houses use computer
controllers to determine when
the fans operate and for how
long. The combination of
controller and air inlets allows
control of how much air enters
the house and where it will
enter and allows good air
quality to be maintained while
minimizing heating costs.
Hot Weather Ventilation:
During hot weather “tunnel ventilation” is used to
keep birds cool. Tunnel ventilation systems consist of
fans at one end of the broiler house and large air inlets
at the opposite end. The fans pull air the length of the
house at a velocity of 500 feet per minute. Tunnel ventilation
removes heat from the building rapidly and
creates a wind chill that provides additional cooling for
the broilers.
When tunnel ventilation alone is not sufficient to
cool the broiler house, the evaporative cooling system
is activated. Energy in the form of heat is used to evaporate
water lowering the air temperature. Originally,
evaporative cooling was accomplished using fogging
systems located inside the house. The fogging nozzles
provided a fine mist of water that evaporated, thus
lowering the air temperature. Occasionally there were
situations when this system was not used correctly. As
a result the air sometimes became saturated and all of
the water did not evaporate, which led to wet litter
problems. This problem was corrected by moving the
evaporative cooling system outside of the house. Fogging
systems were placed on the end of the house
where the air enters. The fogging nozzles sprayed a fine
mist of water onto fluted/perforated pads. The air was
drawn through the pads where water was evaporated
and the air temperature was reduced. This system also
water being wasted as it dripped off the pads.
Recirculating evaporative cooling systems have
become popular as a solution to this problem and is the
primary evaporative cooling system being installed
currently. With this system, water runs through a perforated
pipe at the top of the cool cell pads. Water runs
down and through the pad soaking it. Any water that is
not evaporated is caught in a trough at the bottom of
the pad that delivers the unused water back to a
reservoir to be pumped through the system again.
Depending on environmental conditions (temperature,
humidity), incoming air temperature can be lowered 10
degrees F or more.
Controlling House Environment
Almost all modern broiler houses rely upon electronic
controllers. Through the use of controllers, it is
possible to keep house temperatures within five degrees
of the desired temperature regardless of outside temperature.
This makes it possible to keep the birds comfortable
so they are not diverting energy from growth to
stay warm or cool. The controller monitors house
environmental conditions and adjusts the heating, ventilation
and cooling equipment as necessary to keep
temperatures constant. Today, controllers can monitor
temperature in six or more locations throughout the
house. Humidity can also be monitored, although
adjustments to heaters and fans are usually done on a
temperature basis.
As the house temperature fluctuates, the controller
will turn on the brooders or fans as needed. The controller
operates equipment in the house including:
brooders, fans, inlet machines, curtain machines,
evaporative cooling systems and lights. Many controllers
also allow house conditions to be monitored
remotely.
Using a computer and modem, a grower can call
into the farm and check the temperature and humidity,
as well as, which heaters and fans are operating in all
houses. If needed, changes in the environmental settings
can be made remotely using the computer.
Alarms and Generators
The importance of the maintaining a comfortable
and stress-free environment for the birds cannot be
overstated. Modern broiler housing can provide the
environment needed to optimize broiler performance,
but this is entirely dependent on electricity and the
proper operation of house equipment. It is difficult for a
farm manager to be present 24 hours a day, every day
that birds are in the house. Therefore, it is important to
have an alarm system installed to let the farm manager
know when something goes wrong in the house.
While the system will not correct the problem itself,
its main purpose is the get someone into the house to
evaluate and correct the problem. Alarms are used to
notify if there is loss of power or if the house internal
temperature gets too high or too low in relation to the
desired temperature. The alarm system will activate a
siren, usually located at the facility, to alert anyone
close by and an automatic phone dialer and/or pager to
notify the farm manager while he or she is away from
the farm. In the case of power loss, emergency
generators are used to operate ventilation, feeding and
watering systems to prevent catastrophic losses. The
emergency generator should have the capability of
automatic power switch-over and be capable of
delivering service for extended periods of time to
operate the systems mentioned above.
Summary
Research on improving broiler housing is ongoing.
Energy costs are becoming more significant to the
grower’s bottom line and housing construction, equipment
and operation will be paramount in helping to
make sure the houses are operated as efficiently as
possible. As technology and equipment is redesigned
and developed, researchers will continue to examine
how broiler housing can be heated, cooled, and built in
such a way that modern broilers continue to reach their
genetic potential using the most economical and
efficient methods.
Source: University of Georgia's College of Agricultural and Environmental Sciences, Cooperative Extension service - March 2005