US Poultry Industry Manual - Broilers: Load Out
Learn about the load out processPart of Series:
< Previous Article in Series Next Article in Series >
Editor's Note: The following content is an excerpt from Poultry Industry Manual: The Foreign Animal Disease Preparedness and Response Plan (FAD PReP)/National Animal Health Emergency Management System (NAHEMS) Guidelines which is designed to provide a framework for dealing with an animal health emergency in the United States. Additional content from the manual will be provided as an article series.
Load out is usually done at night or under very dim lighting conditions, which helps keep birds calm during the catching process. Catching broilers at night reduces the probability of scratches, fractured leg or wing bones, and suffocation from piling. Feeder lines, water lines, and other equipment that might interfere with catching crews, or injure birds, need to be raised or removed.
Research has shown that 50% of bruising occurs in the last 3 days that broiler chickens are in houses, so it is vital to avoid injuring birds while catching and loading to minimize condemnations at the plant due to bruising. In 2011, average broiler whole bird condemnations at processing caused by bruising were about 0.001%.
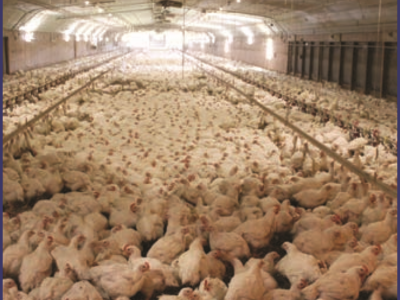
Feed Withdrawal
Withholding feed from broiler chickens immediately prior to catching, loading, and transportation to a processing plant is a standard management practice. Objectives of feed withdrawal are to reduce fecal excretion and external cross-contamination during transportation and to reduce fecal contamination of poultry carcasses that may occur during automated evisceration in a processing plant. During this time, broilers’ crops are emptied of feed and the volume of ingesta in the intestines is markedly reduced, but cecal contents may or may not be evacuated. Integrators provide producers with a load-out time and a detailed feed withdrawal schedule. After 6-10 hours without feed, intestines are flattened and lie low in the body cavity, which allows automated machines to eviscerate the birds without breaking the intestine.
When feed withdrawal time is too short, contamination ensues, causing processing plants to use more water and more labor to process the flock. When feed withdrawal time is too long (greater than 12-14 hours), water can be transferred from muscles to the digestive tract, creating watery intestinal contents and increasing the likelihood of fecal contamination.
Typically, feed is withdrawn approximately 6 hours prior to loading by raising feed lines but broiler chickens should still have access to water right up to catch time to prevent dehydration. Until feed lines are raised, feed should be available in all feed pans to assure that feed withdrawal is done uniformly throughout the flock. However, producers should avoid adding large amounts of finisher feed into the feed system at the start of the withdrawal period and allow birds to clean up feed in pans.
When feed in a pan is down to dust, chickens in a house are out of feed. If only feed dust remains in feeders when feed lines are raised, the broilers have been without feed for longer than the recommended time and correct procedures were not followed. Numbers of Salmonella and Campylobacter in crops and ceca at processing are increased after prolonged feed withdrawal because broilers begin to consume litter and fecal material.
Catching
Broiler chickens can be caught using manual labor or a mechanical harvester. All equipment, including feeders, waterers, brooders, and fans, must be raised to the ceiling or removed from the house before catching begins. Manual catching crews containing 7 or 10 people typically catch between 7,000 and 8,000 chickens per hour. A person catching chickens by hand may lift 5 to 10 tons of broilers during an average shift. Manual catching may result in rough handling and excessive excitement in the flock and be a major cause of injury to the birds. With manual catching, broilers should be caught by two legs, supported by a hand under the breast, and placed (not thrown) into crates.
Mechanical harvester crews usually consist of a team of 4 people who operate 2 catching units, a packing unit, and a forklift. Four people operate as two catching teams, which use independent catching and packing units but share transport trucks. Mechanical catching machines have long rubber fingers that transfer broiler chickens from the surface of the litter to conveyor belts for delivery to a caging system at the rear of the machine.
Mechanical harvesters can catch, batch count, and load up to 8,000 chickens per hour. Chickens are transferred by a short conveyor to packing units which consist of a 5-tier by 3-drawer packing module. Forklifts transfer loaded packing modules to a transport truck that usually holds 20 modules stacked 2 high. Approximately 6,000 broiler chickens are loaded on each truck. When operated correctly, mechanical harvesters require no human contact with the chickens and reduce bruising and other causes of downgrading.
Producers are encouraged to be present during load-out to verify that the chickens are loaded carefully. During loadout, producers are encouraged to walk the house with the loading crew foreman to do a final check for dead birds.
If broilers die right before or during load-out, they should be loaded onto the truck to be counted in the final weight. Each load of chickens is weighed immediately on arrival at the processing plant and this weight will be used to determine the producer’s pay.
Reference: "USDA APHIS | FAD Prep Industry Manuals". Aphis.Usda.Gov. 2013. https://www.aphis.usda.gov/aph...
The manual was produced by the Center for Food Security and Public Health, Iowa State University of Science and Technology, College of Veterinary Medicine, in collaboration with the USDA Animal and Plant Health Inspection Service through a cooperative agreement.