US Poultry Industry Manual - Broilers: scope of the broiler industry
US broiler production scale and scopePart of Series:
Next Article in Series >
Editor's Note: The following content is an excerpt from Poultry Industry Manual: The Foreign Animal Disease Preparedness and Response Plan (FAD PReP)/National Animal Health Emergency Management System (NAHEMS) Guidelines which is designed to provide a framework for dealing with an animal health emergency in the United States. Additional content from the manual will be provided as an article series.
Broiler chickens are bred and raised for meat production. The broiler industry is the most advanced system of animal food production, and the United States has the world’s largest broiler industry. In 2012, data released by the National Chicken Council indicates that the broiler industry provides over 1 million jobs, $47 billion in wages, $197 billion in economic activity, and $17.2 billion in government revenue. Today’s broiler industry consists of around 40 vertically integrated companies which contract with about 29,500 farmers who produce 95% of this nation’s broiler chickens. About 5% of broilers are produced on company-owned farms. Since 2009, foreign ownership of US broiler companies has increased and now accounts for an estimated 25% of total production. The largest broiler companies, Tyson Foods and JBS-owned Pilgrim’s Pride are transnational, multi-animal protein companies with global marketing and distribution of their products. The top five broiler companies in this country are listed in Table 1 below.
Table 1 |
Leading Broiler Production Companies (2012) |
||
National Ranking |
Company |
Headquarters Location |
Estimated Market Share (%) |
1 |
Tyson Foods, Inc. |
Arkansas |
27.1 |
2 |
Pilgrim’s Pride |
Colorado |
24.1 |
3 |
Sanderson Farms |
Mississippi |
9.2 |
4 |
Perdue Farms |
Maryland |
8.9 |
5 |
Koch Foods, Inc. |
Illinois |
7.8 |
Broiler Numbers and Location
Approximately 9.0 billion broiler chickens are produced in this country each year with a combined live weight of 50 billion pounds resulting in the annual marketing of 36.5 billion pounds of chicken products on a ready-to-cook basis. Broiler chickens are marketed at an average age of 47 days with an average live weight of 5.80 pounds. The target weight of broilers at processing may be more or less than the average live weight, depending on the market and requirements of the processing plant. Average feed conversion of broiler chickens is 1.91 and average mortality from placement to marketing is 3.8%. The broiler industry in the United States is concentrated in the Southeast, due to a favorable climate and proximity to grains and final markets. The top five broiler-producing states are listed in Table 2 below.
Table 2. Leading Broiler Production States (2012) |
||
National Ranking |
State |
Billions of Broilers |
1 |
Georgia |
1.362 |
2 |
Alabama |
1.004 |
3 |
Arkansas |
0.977 |
4 |
North Carolina |
0.800 |
5 |
Mississippi |
0.751 |
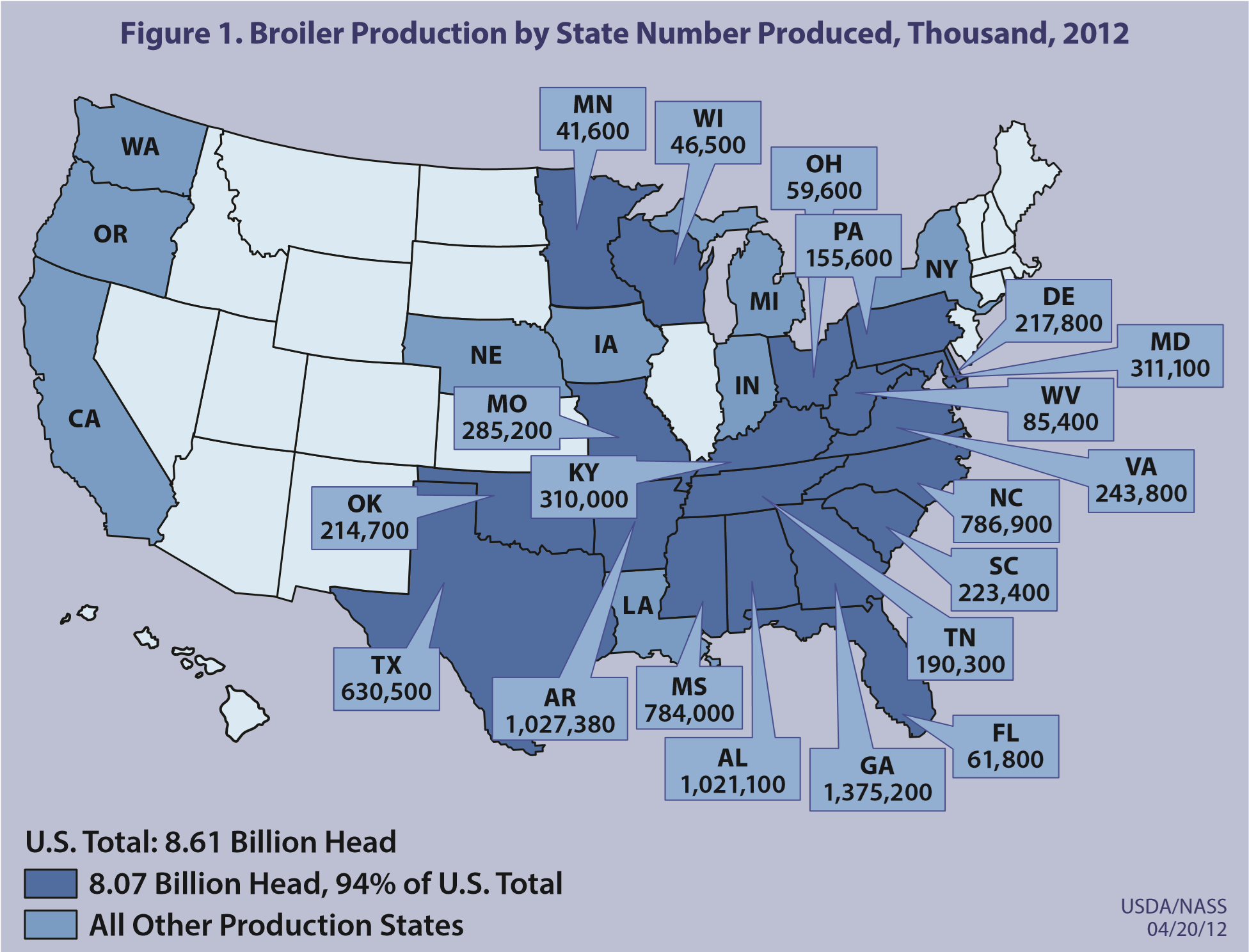
INDUSTRY STRUCTURE
Contract Production
During the 1950s, contract growing of broiler chickens began in response to farmers losing their farms due to risks associated with financing chicks and feed. Consequently, feed companies, hatcheries, and others began to provide financing and credit for growing broiler chickens. Contractors (financiers) assumed most of the financial risk and profits were shared between the financier and the contract grower. Today, vertically integrated broiler companies are the primary contractors; independent contract growers produce 95% of broiler chickens. Broiler companies furnish chicks, feed, medication, flock supervision, and labor and equipment for catching and transporting broiler chickens from the farm to the processing plant. Growers furnish houses, equipment (feeders, waterers, brooders, and fans), water, electricity, fuel, litter, and labor and follow management protocols specified by the processing company (integrator).
Chickens belong to the integrator, not the contract grower. However, when a chicken dies, proper disposal of the carcass is the responsibility of the grower. Contract growers are dedicated to a specific company and specific processing plant and are usually paid based on the number of pounds of live broiler chickens delivered to the processing plant and production efficiency parameters including feed conversion ratio and overall cost of production. Growers should visit each flock twice daily to remove moribund or dead birds, adjust the height of feeders and waterers, check for proper ventilation, and monitor litter moisture content to avoid excess ammonia production.
Vertical Integration
Before 1950, the broiler industry consisted of tens of thousands of small businesses. With the advent of vertical integration in the 1950s, those thousands became an industry of hundreds. Vertical integration is a business arrangement wherein multiple stages of the production and marketing system are owned by one enterprise. By the mid-1960s, over 90% of broilers came from integrated farms. During the ensuing years, consolidation resulted in merging of companies to form the 40 odd companies that comprise today’s industry. Vertically integrated broiler companies own breeder flocks, hatcheries, chickens in the broiler houses, feed mills, processing plants, and a fleet of trucks. Trucks are needed to transport chicks from hatcheries to farms, feed from the feed mill to farms, broiler chickens from farms to the processing plant, and often product to buyers.
Vertical integration allows coordination of capacities at each stage of production and creates one profit center. This system allows a high degree of control over how broiler chickens are raised, fed, and processed and results in use of the best available technology and management to produce and process chickens. An integrated broiler operation, usually referred to as a complex or division, typically has a centrally located hatchery, feed mill, and processing plant that coordinate with pullet, breeder, and broiler farms.
Processing plant capacity determines the number of farms required to provide a steady supply of chickens for the plant and the size of the feed mill needed to provide feed for chickens and breeders on those farms. Transportation costs associated with moving feed are significant and many companies require contract grower farms to be located within a 10-30 mile radius from the feed mill. Production and processing of 1 million broilers per week with an 8-week cycle requires 400 houses with an average capacity of 20,000 broilers. A typical broiler farm has four houses.
Integrators closely monitor factors affecting cost of production down to hundredths of a cent per pound. These factors include morbidity, mortality, rate of daily gain, feed conversion, and condemnations. Company veterinarians constantly monitor flocks for disease problems, which are quickly identified and corrected. Integrated companies are closed marketing systems and do not buy or sell birds in open livestock markets. There is little crossover of birds, people, or equipment between farms and between companies.
Broilers are produced under single-age, all-in all-out production schemes which break the chain of disease transmission from one flock to the next. Extensive biosecurity programs limit access to poultry houses and encourage use of dedicated clothing and boots, discourage sharing of equipment, and prohibit contact with other birds including pets and other poultry.
Service Technicians
Service technicians are a critical part of broiler flock husbandry. Service technicians are employed by the integrator and act as a liaison between contract growers and company management. Company expectations and policy changes are presented to the growers by service technicians. Service technicians assist with scheduling chick arrivals, feed deliveries to farms, and final load-out for processing. Typically, service technicians visit each farm weekly and provide advice on best management practices for the strain of broiler chicken being grown to achieve the company’s target market weight.
Responsibilities and Monitoring
Measurements are taken at specific times during grow-out and are monitored to evaluate flock health and progress. These measurements include water and feed consumption, mortality rates, and body weights. As flocks approach market weight, service technicians spot-weigh broilers and calculate the average rate of daily gain. This information, along with current health of the flock, is used to schedule flocks for processing. An unexplained decline in water consumption paired with a drop in feed consumption may indicate a disease challenge or equipment malfunction. Early investigation of flock problems by the grower and service technician is necessary to prevent large-scale problems from developing, and communication between the two is important.
Health Maintenance
Service technicians work with company veterinarians to diagnose and treat diseases. Service technicians typically perform on-site necropsies on several birds to help determine a disease diagnosis. Once a disease has been diagnosed and the company veterinarian has been consulted, field technicians determine the best way to handle the particular disease situation and may administer medication via water or feed and make recommendations to the grower.
Reference: "USDA APHIS | FAD Prep Industry Manuals". Aphis.Usda.Gov. 2013. https://www.aphis.usda.gov/aph...
The manual was produced by the Center for Food Security and Public Health, Iowa State University of Science and Technology, College of Veterinary Medicine, in collaboration with the USDA Animal and Plant Health Inspection Service through a cooperative agreement.