Test day at Bess Labs
Testing fans at the Bioenvironmental and Structural Systems LaboratoryIf you are involved in buying or selling agricultural fans, chances are you are familiar with BESS Labs. For 34 years, BESS Labs, also known as Bioenvironmental and Structural Systems Laboratory, has been the go-to source of unbiased fan data for both producers and manufacturers. I recently got to join one of Hog Slat's engineering teams for a testing session at the University of Illinois campus.
On the day of our scheduled session, we arrived at BESS Labs on a bright but freezing cold day. As the engineers prepared the first test fan, I asked lab manager Steve Ford about the lab's origins.
Steve said, "In the late 1980s, a group of Wisconsin electric coops wanted to develop a rebate program to encourage the use of energy-efficient fans. However, they discovered that the cfm/watts data required to create the rebate program was unavailable. Subsequently, the coop personnel contacted the university's engineering department to perform the necessary tests. For the initial testing in 1990, the coop purchased 40 fans from multiple vendors and shipped them to Champaign."
Steve explained that BESS Labs has tested as many as 900 fans in a year, but on average, they test between 500 and 600 fans annually. Fans come from manufacturers worldwide, including fans not designated for sale in the US. The testing done by BESS Labs provides foreign manufacturers with confirmed data accepted throughout the world.
So, what is a wind tunnel?
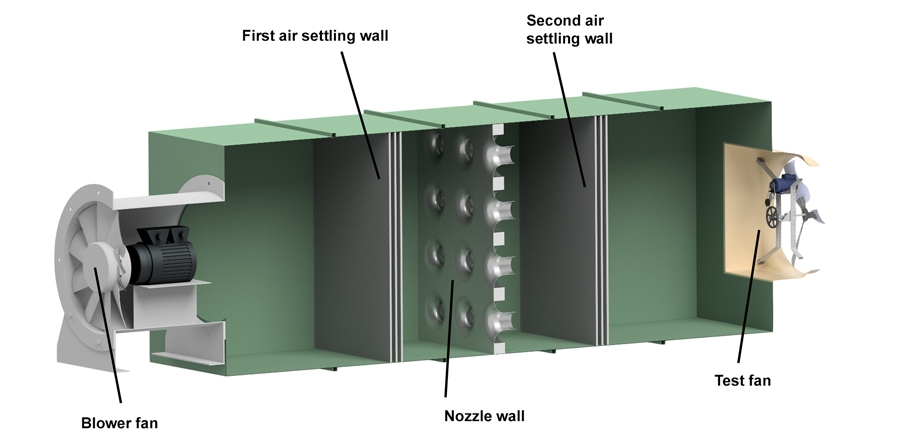
The BESS Lab unit is a 9' x 9' x 26' long wooden chamber. To begin the test, the team fastened the test fan at one end of the chamber and warmed up the motor for 15 minutes.
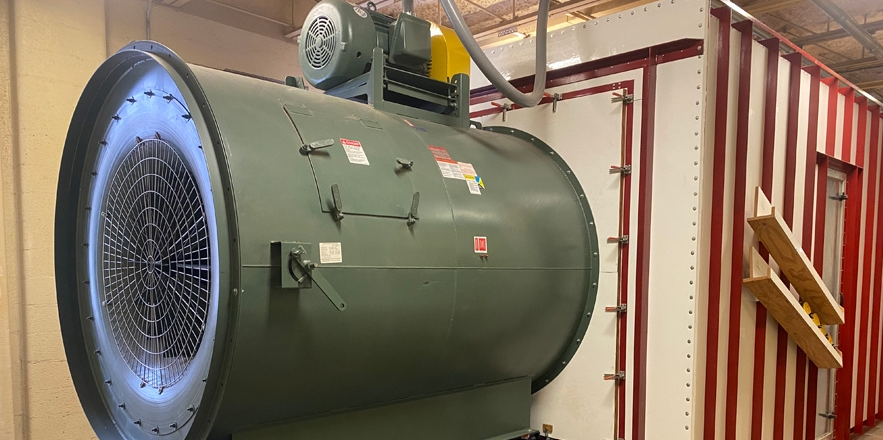
Then, a 50 HP variable speed blower fan at the other end pushed air through a honeycombed mesh wall called an air settling screen to even out the flow.
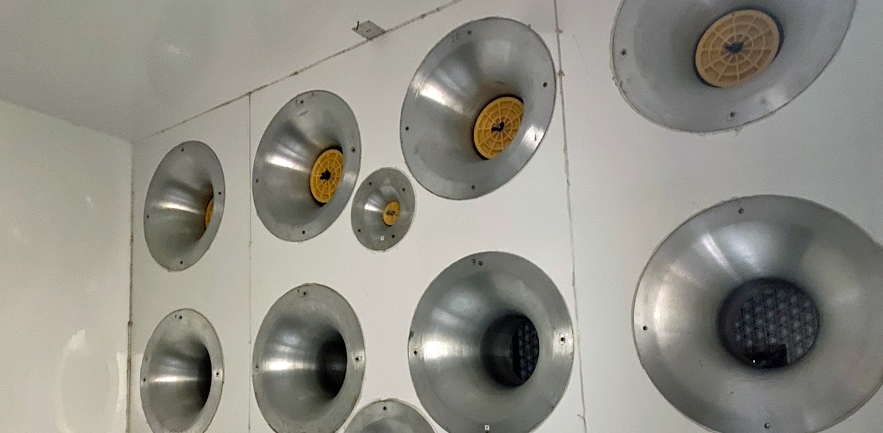
Next, the air passed through a wall of precisely calibrated nozzles with a specific cross-sectional area. Sensors on each side of the nozzle wall recorded the pressure drop as air passed through the nozzles to determine the amount of cfm being moved. The air then passed through a second air settling wall before reaching the test fan. Steve varied the speed of the blower fan to test airflow at typical negative pressures such as .05, .10, .15, etc. Additional sensors also recorded power consumption at each stage.
Our session included verifying air delivery and efficiency for 36, 54, and 57-inch fans with different prop, motor, and pulley combinations. The engineers were particularly interested in the results of the OMNI motor drive powering a new fan series scheduled for release later this year. The test confirmed the expected efficiency and precise speed regulation, along with considerable improvements in motor protection.
The couple of days spent at BESS Labs proved to be an insightful experience in the fan testing process. Undoubtedly, their unbiased platform over the past decades has driven the efficiency improvements seen in the fans used by the livestock and poultry industries.